Introduction to Water Filtration – Part 3
Introduction to Water Filtration - Part 3
Automatic Gravity Filters
Many manufacturers have developed gravity filters that are automatically backwashed at a preset head loss. Head loss, water level being above media, motivates a backwash siphon and pulls wash water from storage up through the bed and out the siphon pipe to waste. A low level in the backwash storage cracks the siphon and the filter resumes service.
Automatic gravity filters are available in diameters of up to 15 feet. If they are outfitted with a high-rate, multi-layer media, a single large-diameter unit can filter as much as 1,000 GPM.
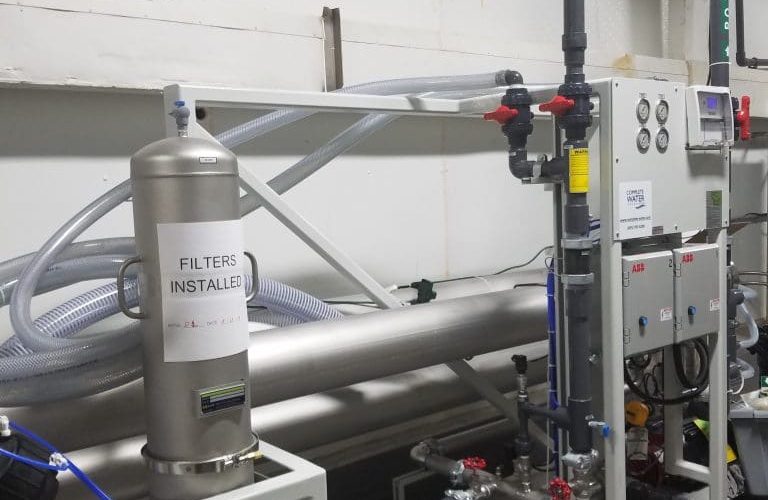
Pressure Filters
Pressure filters are normally used with a hot action softeners to allow high-temperature operation and to avoid heat loss. When working with pressure filters you eliminate the need for re-pumping of filtered water. Pressure filters are similar to gravity filters in that they contain filter media, an underdrain system, a supporting bed, and a control device. To note, the filter shell does not have wash water gutters.
Both horizontally and vertically built pressure filters contain cylindrical steel shells and dished heads. A horizontal pressure filter can have capacities from 200 to 600 GPM that are roughly 8 feet in diameter and about 10 to 25 feet long. A vertical pressure filter can have a capacity of 300 GPM with filtration rates of 3 GPM/ft² and range in diameters of 1 to 10 feet. These filters are divided into sections allowing individual backwashing. Backwash water can go back to the softener or clarifier for recovery.
Pressure filters typically are used at a service flow rate of 3 GPM/ft². Multimedia or dual filters are constructed for 6-8 GPM/ft². At medium temperature, filter backwash has a recommended rate of 6-8 GPM/ft² for anthracite and 12-15 GPM/ft² for sand. Anthracite filters combined with hot process softeners need a backwash of 12-15 GPM/ft² due to the water being less dense at high operating temperatures. Cold water should not be utilized to backwash a hot process filter. Doing this, would cause expansion and contraction of the system metallurgy. In turn, that would lead to metal fatigue and having the oxygen-burdened cold water to speed up corrosion.
Gravity Filters
Gravity filters are open liners that rely on system gravity head for operation. Besides the filter media there are several key components of a gravity filter.
- Â Filter Shell: It can be either concrete or steel and come in shapes of squares, rectangles, or circles. The most commonly used are rectangular reinforced concrete units.
- Support Bed: This will avert the loss of fine sand or anthracite through the underdrain system. It is typically 1 to 2 feet deep and distributes backwash water.
- Underdrain System: It will provide uniform collection of filtered water and uniform distribution of backwash water. This typically will consist of a header and laterals, with strainers or perforations spaced appropriately. False tank bottoms with suitably spaced strainers can also be used for underdrain systems.
- Wash Water Gutters: These are big enough to compile backwash water without flooding. They are spaced out to ensure that the horizontal travel of backwash water will not surpass 3-3 feet. In usual sand bed units, wash gutters will be placed about 2 feet above the filter surface. Adequate freeboard needs to be supplied to prevent the loss of a portion of the filter media when the operation is at maximum backwash rates.
- Control Devices: These will maximize filter operation efficiency. Flow rate controllers are operated by venturi tubes in the effluent line and automatically hold consistent delivery of filtered water. Backwash flow rate controllers can also be utilized. The flow rate and head loss gauges must be used properly for efficient operation.