Boiler Failures Due to Corrosion – Part 5
Boiler Failures Due to Corrosion – Part 5
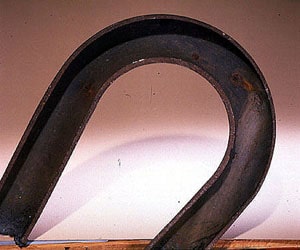
Superheater Tubes
Some boiler failures due to corrosion may be the result of superheater tube failures. Superheater tube failures are caused by a number of conditions, both mechanical and chemical. In any instance of superheater tube failure, analysis of the deposits found is an important factor in solving the problem. Magnetic oxide deposits at the point of failure, like in the image on the left, are a direct indication of oxidation of the tube metal. When the deposits found in the area of failure are primarily iron oxide, it may be necessary to explore a number of operating conditions in order to determine the initial cause.
Oxidation may occur if the flow of steam through the tubes is restricted or if the heat input is excessive, permitting overheating. In the case of insufficient steam flow, the restriction may be due to conditions prevalent during the transition periods of boiler start-up or shutdown. This occurs if adequate precautions have not been taken to protect the superheater during the transition periods.
Soluble-salt deposits may form at a superheater tube inlet as a result of excessive entrainment of boiler water solids with the steam. This can result in restricted flow. In some cases, there is a very clear delineation between oxidation products in the hot area and soluble-salts deposits at the inlet. However, in most occurrences, a high percentage of sodium salt deposits is found in the hot areas along with the oxidation products. There is little doubt in such instances that boiler water carryover has contributed to the problem.
It is essential that the manufacturer’s instructions be followed rigidly to prevent overheating problems during start-up or shutdown and to prevent oxygen corrosion during downtime.
Boiler Design Problems
Certain basic design flaws can contribute to tube failures. Problems which occur as a result of a design flaw can also be intensified by the boiler water chemistry. The boiler water often contains elements that become corrosive when concentrated far beyond normal values as a result of design problems. For example, many industrial boilers are treated in such a manner that low concentrations of caustic soda are present in the boiler water. The caustic can become corrosive to steel when the boiler water is allowed to concentrate to abnormally high values as a result of poor design. Roof tubes, nose arch tubes, and convection pass tubes with slopes of less than 30 degrees from the horizontal are more subject to deposition and stratification problems and tube failures than vertical tubes. The use of horizontal hairpin tube configurations with inadequate forced circulation of water through the tubes often permits stratification of steam and water. This can lead to steam blanketing or caustic corrosion problems.
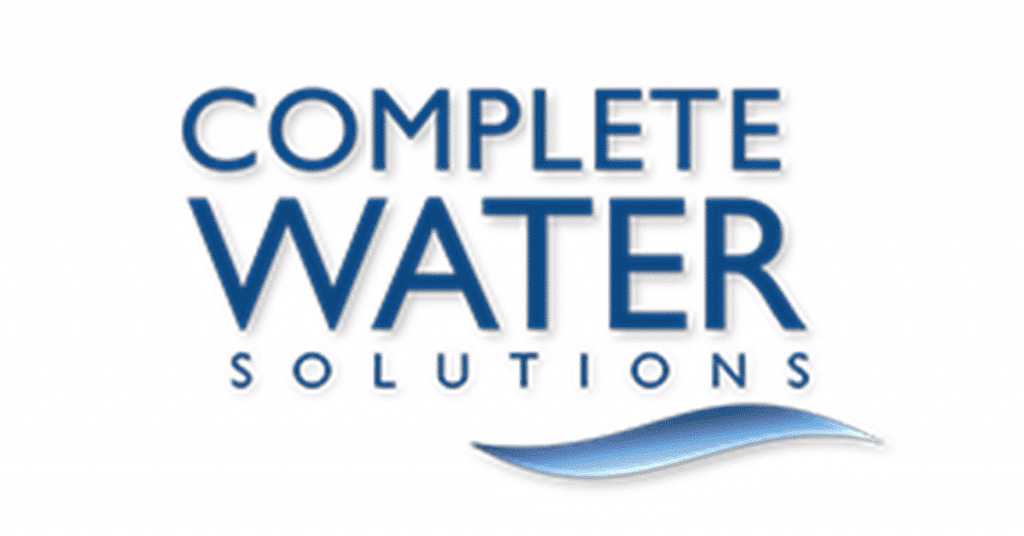